設計した部品やアセンブリに対して、強度や剛性が許容値範囲内か確認するために、構造解析をしたいという場面があるかと思います。
SOLIDWORKS PremiumのライセンスやSOLIDWORKS Simulationのアドインをお持ちの方は、SOLIDWORKS Simulationの機能を使用することができます。
SOLIDWORKS Simulationでは、作成した3Dモデルに対して、有限要素法(FEM)による構造解析を行うことができます。
SOLIDWORKS Simulationを用いて構造解析をすることで、手計算では難しいような形状の計算でも、発生応力や変形量を確認することができます。
大きな力が加わる部品や、高い剛性が求められるような部材は、簡易的にでも構造解析を行うことをおすすめします。
条件設定や結果の考察など、難しい場面もありますが、丁寧に解説しますので、ぜひ最後までお読みいただければと思います。
特に、本記事では、結果を正しく評価するために、「解析の妥当性を評価する」方法について記載しています。
もくじ
解析実行後の作業
第2部の条件設定編、第3部のメッシュ編までの解析手順を踏めば、解析を実行することができます。
解析実行後は、解析結果の考察を行います。
解析結果を表示して各指標値を確認し、その解析の妥当性を評価し、設計上の安全性を含めた機能性を評価し、それらを踏まえて実設計に反映させるというフェーズになります。
それぞれどういったことをするのかを以下で詳しく説明します。
解析結果の確認
まずは、解析結果を画面表示して、応力や変位量などを確認していきます。
強度解析において、確認すべき主な項目は以下の4点です。
- 応力(X方向、Y方向、Z方向応力、主応力)
- 変位量(X方向、Y方向、Z方向変位、合成変位)
- ひずみ(X方向、Y方向、Z方向、合成ひずみ)
- 変形挙動
解析結果の妥当性の評価
解析結果を確認しながら、解析結果が妥当なものなのかを評価・判断する必要があります。
構造解析は、解析条件が適切でないと、求めたい解析結果が得られません。
また、解析には必ず誤差があり、現実と解析で必ず乖離が生じます。
解析結果はあくまで近似解です。厳密解ではありません。
そういったことを踏まえて、得られた解析結果(=近似解)が、求めたい解析結果(=厳密解)とどの程度近しいかを判断します。
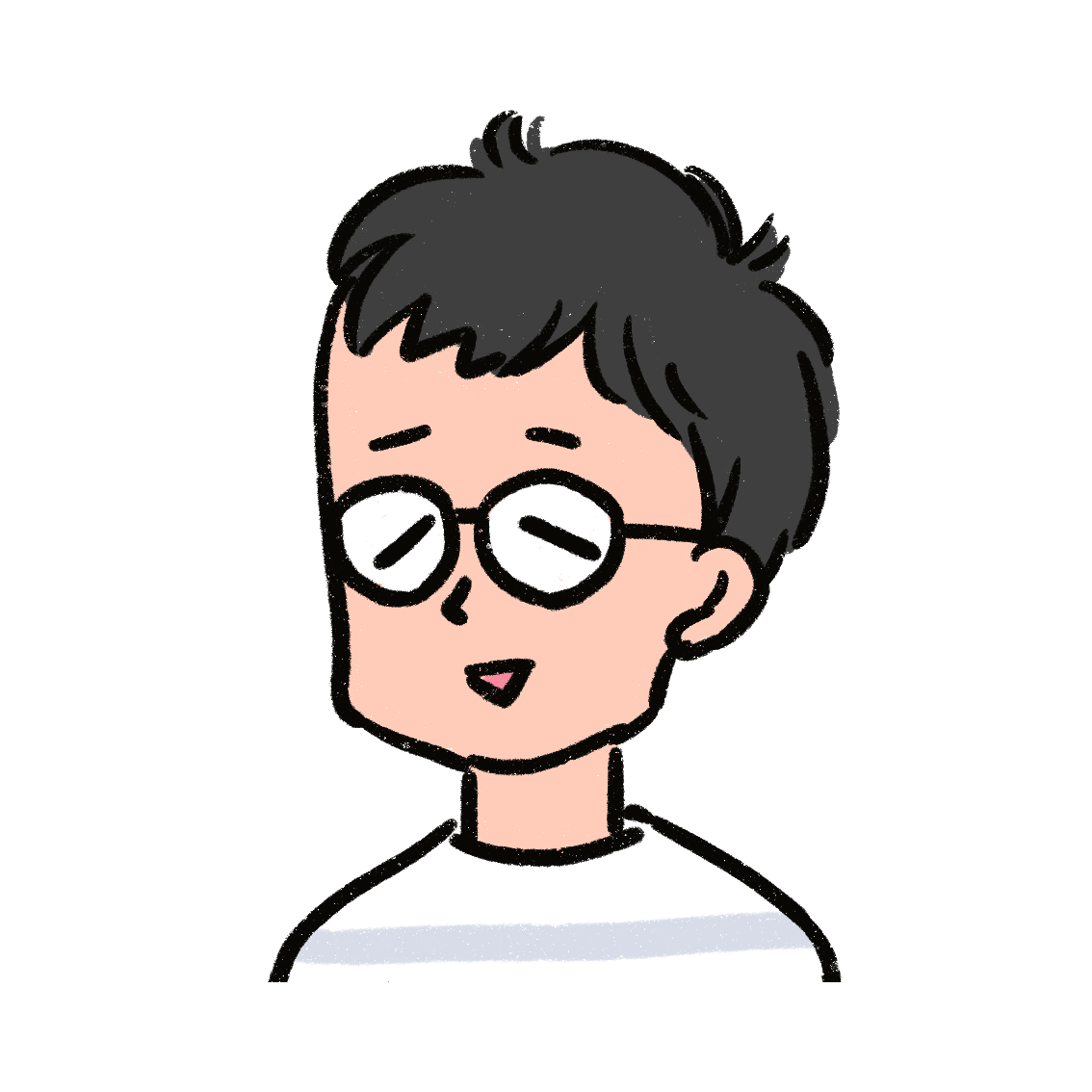
解析できたからと言って、解析結果を鵜呑みにしてしまうと危険です。
妥当性を評価して、解析結果が信頼できるものかを確認しましょう。
妥当性評価の判断材料
解析の妥当性を判断するには、以下の項目に注視します。
- 変形挙動の確認
- メッシュサイズの確認
- 手計算によるオーダー確認
変形挙動の確認
SOLIDWORKS Simulationでは、変形挙動を動画で確認することができます。
変形の起点や変形時の形状、応力の立ち方など、動画でその移り変わりを確認することができます。
変形の移り変わりを確認して、不自然な変形をしたり、想定と全く異なる変形をしたりする場合は、解析条件が間違っている可能性が高いです。
解析条件をもう一度見直して確認してみましょう。
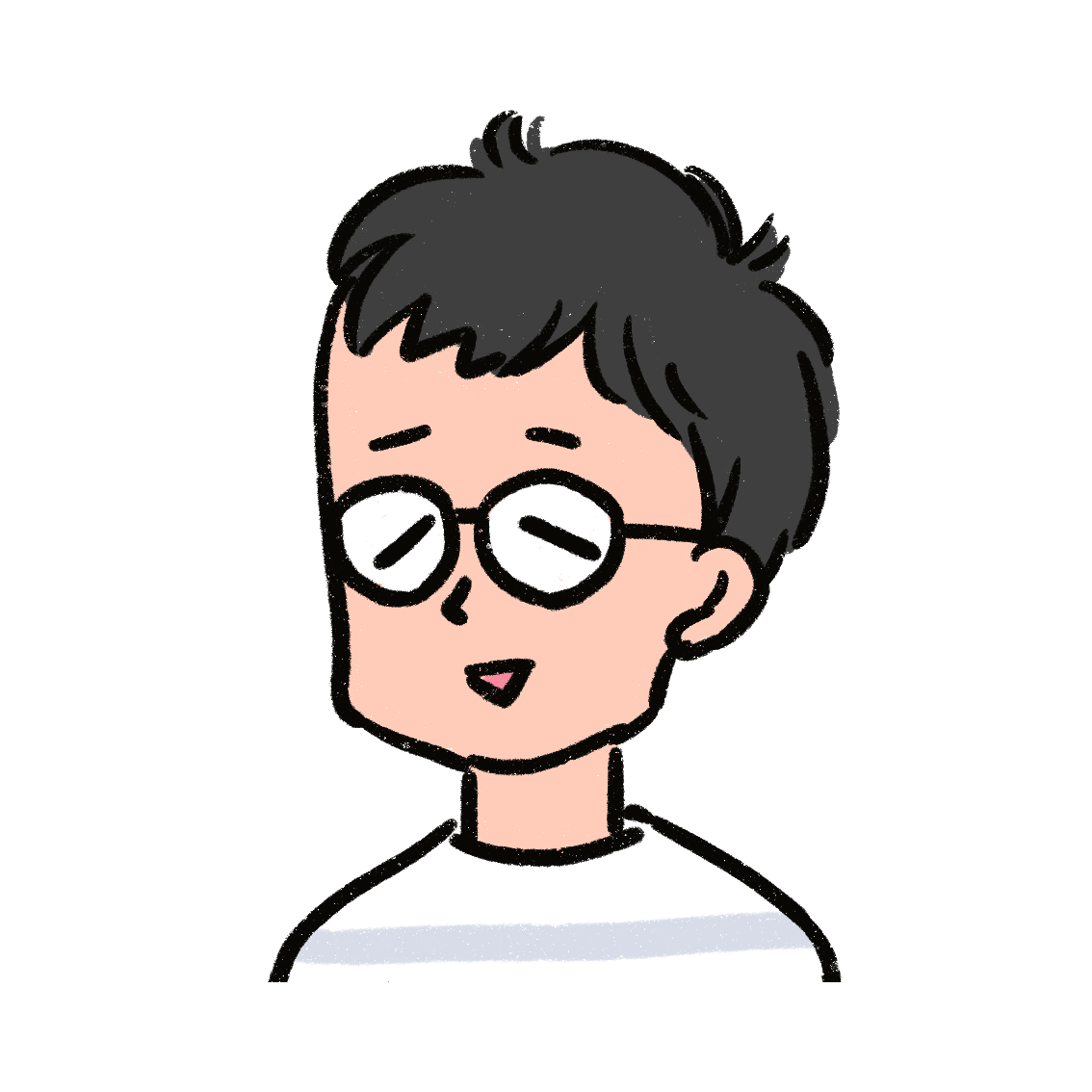
拘束条件や接触条件に設定ミスがある可能性が高いです。
設定の間違いや設定モレしている条件がないか確認しましょう。
メッシュサイズの確認
第3部のメッシュ編でも述べましたが、メッシュの設定が適切でないと、適切な解析結果が得られません。
中でも、メッシュサイズが解析精度に大きく影響します。
メッシュサイズが適切かを判断するには、解析結果の変位量を確認しましょう。
有限要素解析では、接点の変位をもとに、フックの法則より応力を求めます。
そのため、変位量が間違った値であれば、応力も正しい値になりません。
フックの法則 \(\sigma=E\epsilon\)( \(\sigma\):応力、\(E\):ヤング率、\(\epsilon\):ひずみ )
メッシュサイズの妥当性を確認する方法として、解析条件はそのままで、メッシュサイズのみを変えて再解析してみます。
具体的には、以下の手順で追加解析をしていきます。
- 当初の設定した条件、メッシュサイズで解析
- メッシュサイズのみを半分にして、それ以外は❶と同一条件で再度解析
- ❶と❷の最大変位量の差を計算する
- ❸が閾値以下であればOK。
- 閾値以上の場合は、更にメッシュサイズを半分にして再度解析。
メッシュサイズを細かくしていくと、変位量や応力は収束していきます。
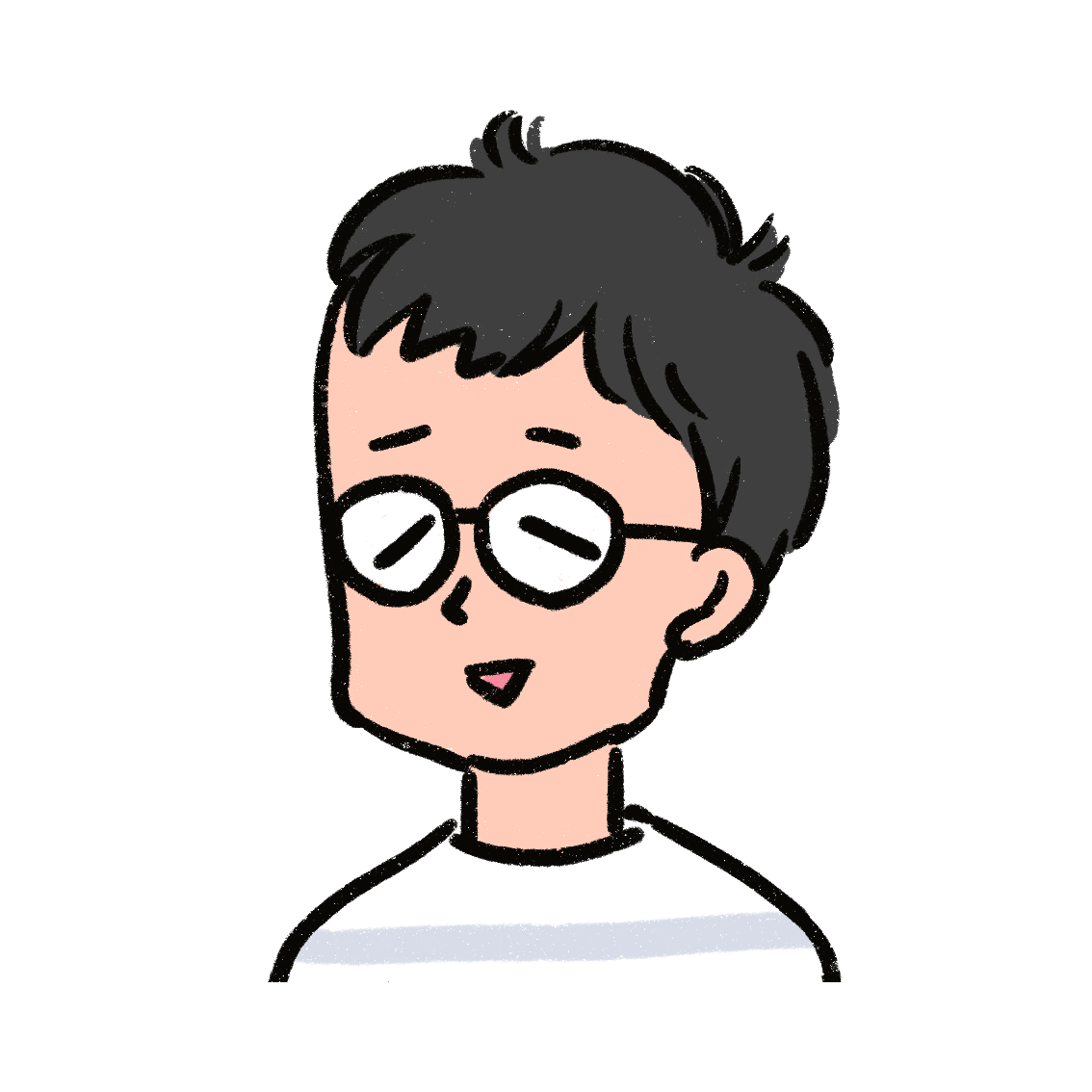
閾値の決め方は解析者によって異なります。
筆者の場合、5%程度の閾値に設定する場合が多いです。
手計算によるオーダー確認
応力や変位量を、手計算で算出したものと、解析結果とを比較してみます。
単純な梁のような簡単な解析モデルであれば、手計算でも計算できるかと思います。
しかし、複雑な形状や複雑な条件の場合は、手計算するのも難しいです。
手計算が難しい複雑な解析モデルの場合は、手計算できるくらいの形状に大胆に簡易化してもいいでしょう。
簡易化している場合は、当然、手計算と解析結果で値が変わります。
しかし、オーダーが変わるほど、そこまで大きくは変わりません。
手計算の結果と解析結果とで、オーダーがおおよそ合っていれば、妥当性は高いといえるでしょう。
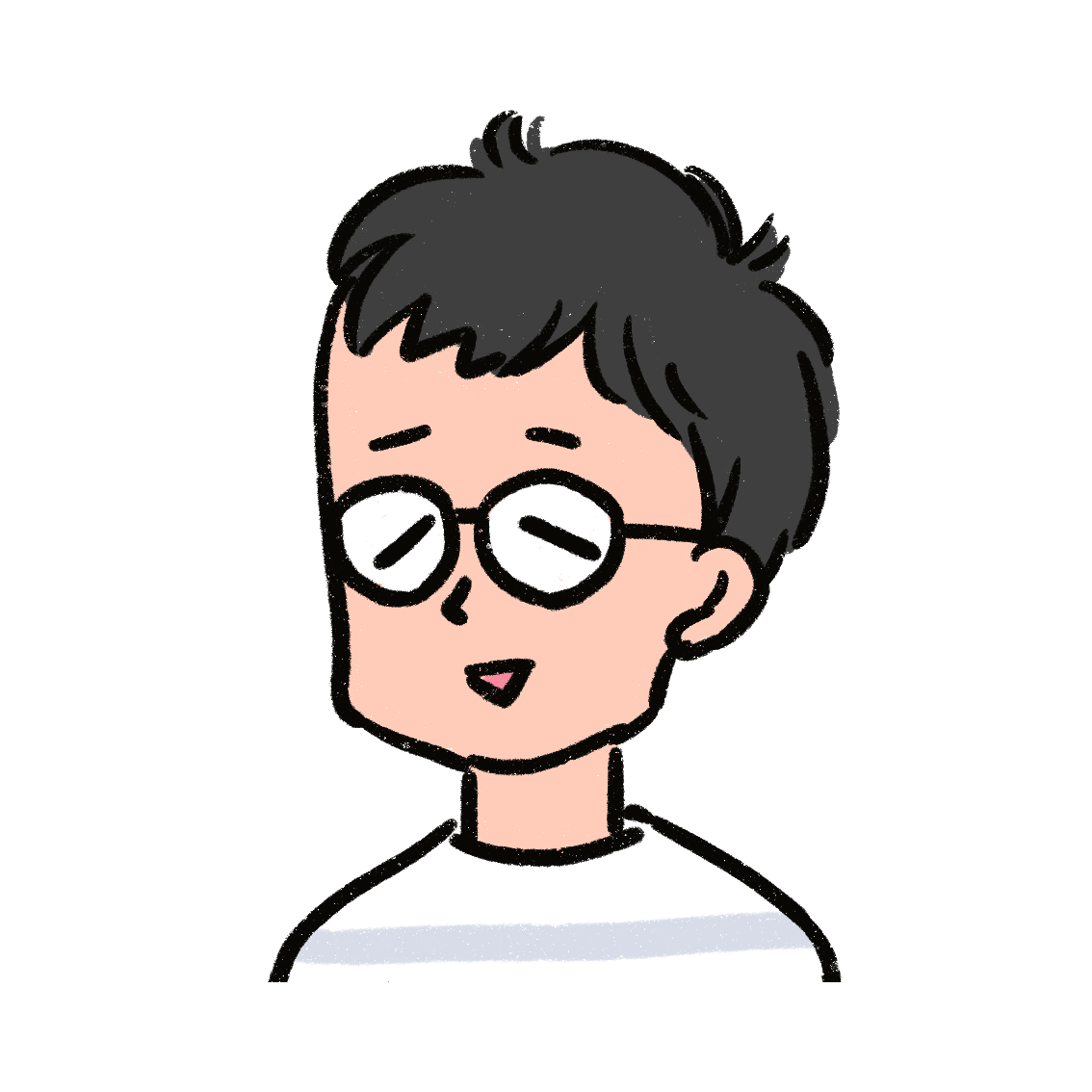
補足:オーダーとは、工学などでよく使われる言葉で「大体このぐらいの桁の大きさ」という意味です。
反対に、手計算の結果と解析結果とで桁数が2つも3つも異なるような場合は、解析結果の妥当性を疑った方がいいかもしれません。
特異点の判別
解析結果を鵜呑みにできない理由の一つに、「特異点」があります。
特異点とは、メッシュの形状的によって起きるひずみ現象で、周囲に対して局所的に高い応力が発生する現象です。
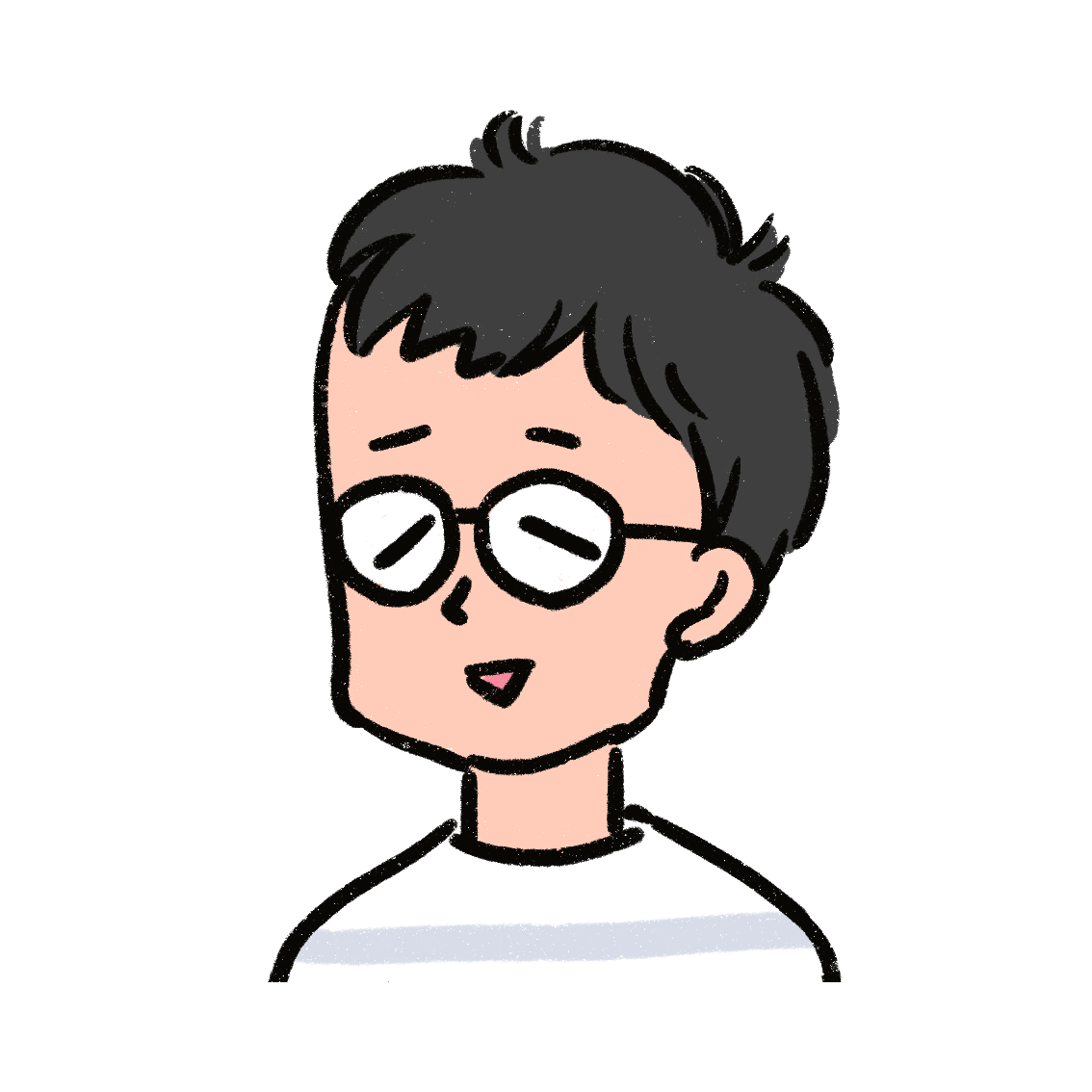
特異点は、実際には起きない解析特有の現象です。
しかも、特異点では、メッシュを細かくすればするほど、応力値が収束せずに大きくなっていきます。
似たような現象で、「応力集中」があります。
応力集中とは、構造物や部品の一部に応力が局所的に発生する現象です。
構造物に穴や切欠きなど、断面形状が急に変化する部分で発生します。
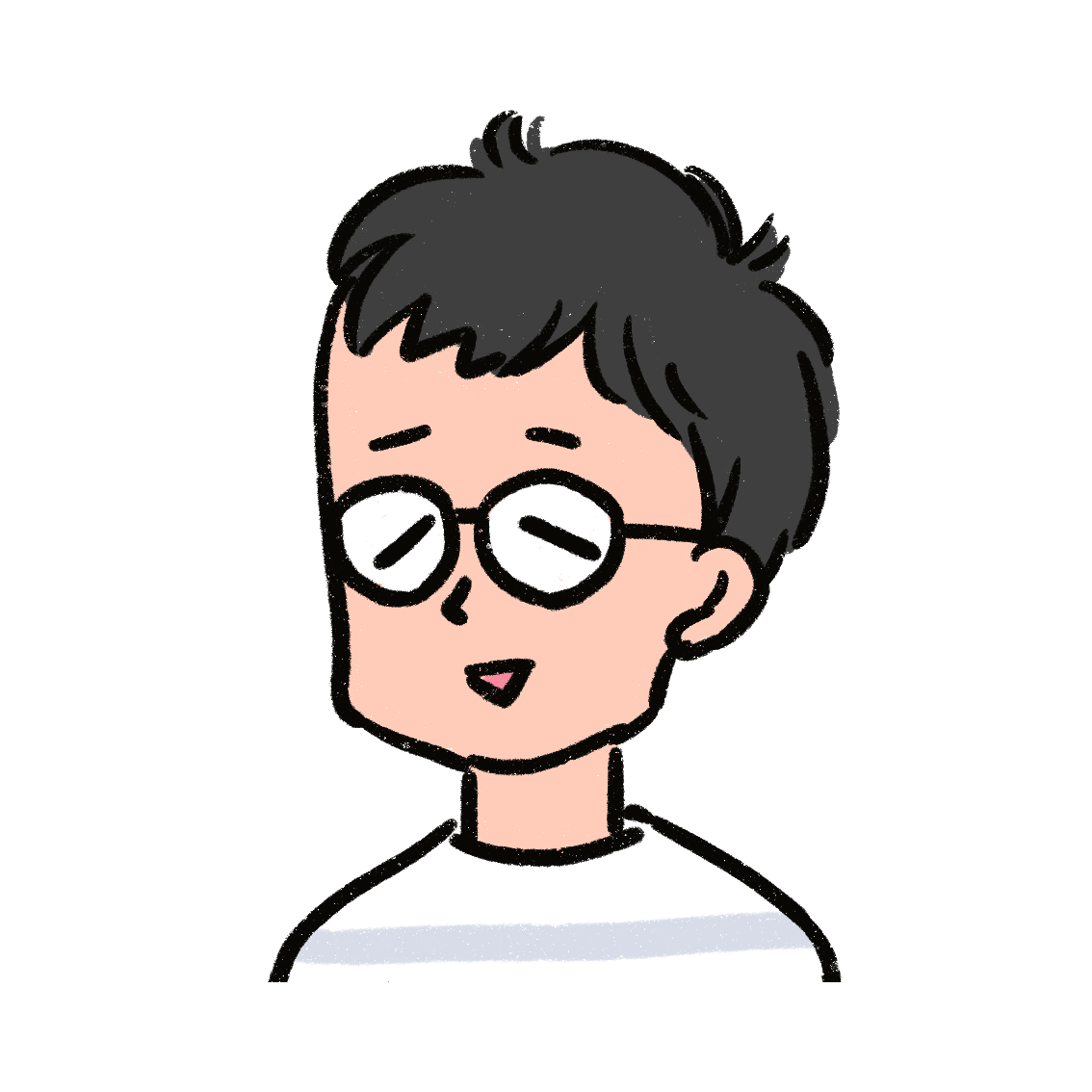
応力集中は、実際に起きる現象です。
解析結果を評価する際には、応力集中と特異点を判別する必要があります。
特異点を見分けるポイント
特異点は、主に以下のところに発生します。
- 隅Rがゼロの地点
- 拘束条件を付与した地点
- 集中荷重を付与した地点
隅Rがゼロの地点
解析モデルの隅Rがゼロとなる地点では、特異点による高い応力が発生します。
ですが、実際の現象でも、隅部は応力集中が発生しやすい箇所になります。
特異点を解消するには、応力の高い隅部にフィレット(R加工)を追加します。
3Dモデルに隅Rを付与することで、メッシュ形状によるひずみが解消され、応力値を収束させることができます。
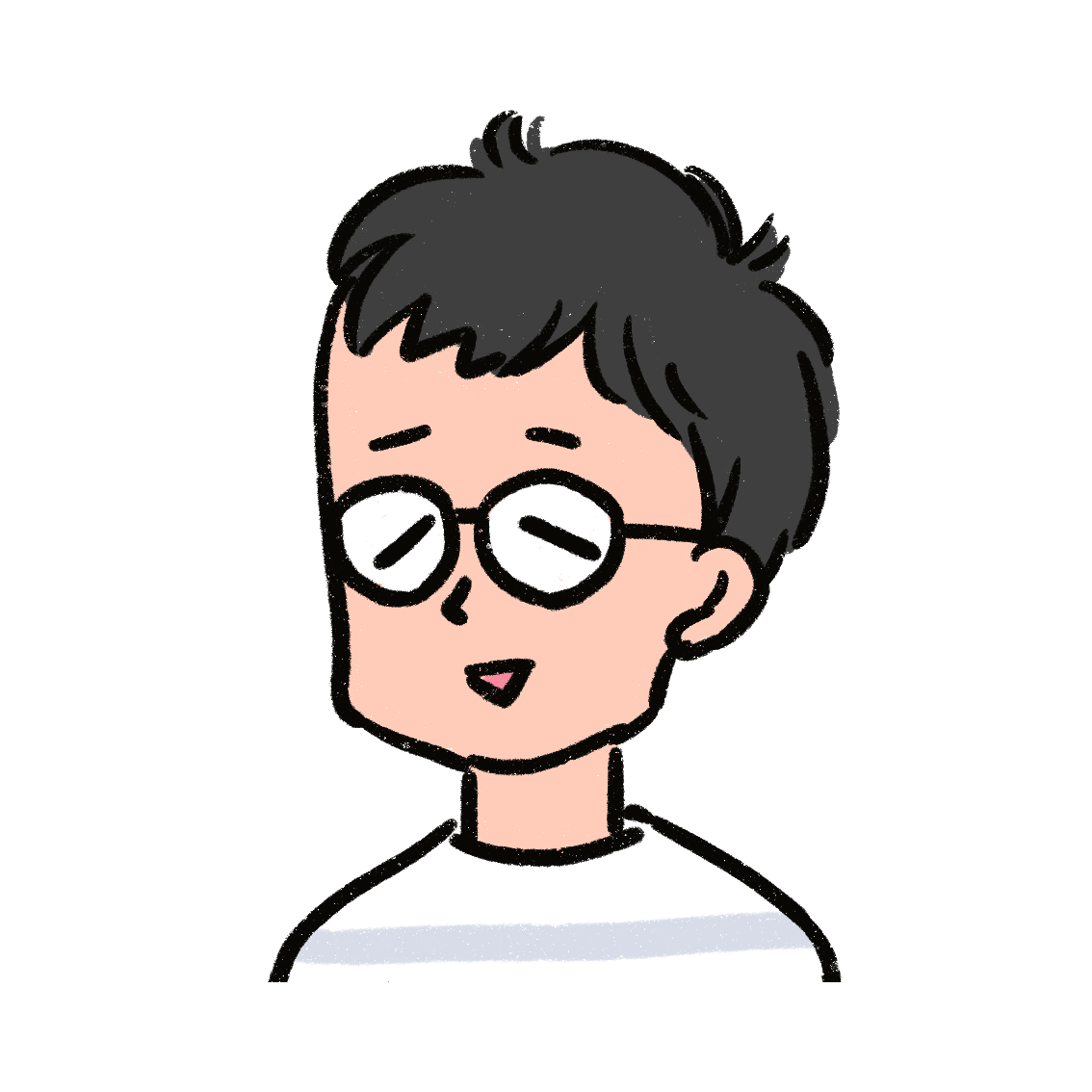
隅部に発生する特異点は、隅Rを追加して解消してあげましょう。
拘束条件を付与した地点
構造解析する際には、どこかの面や辺を固定する必要があります。
固定条件を付与した地点の近傍は、固定部と変形部の境界となるため、特異点による高い応力が発生します。
この場合、実際には発生しない応力ですので、解析結果に含めないようにしましょう。
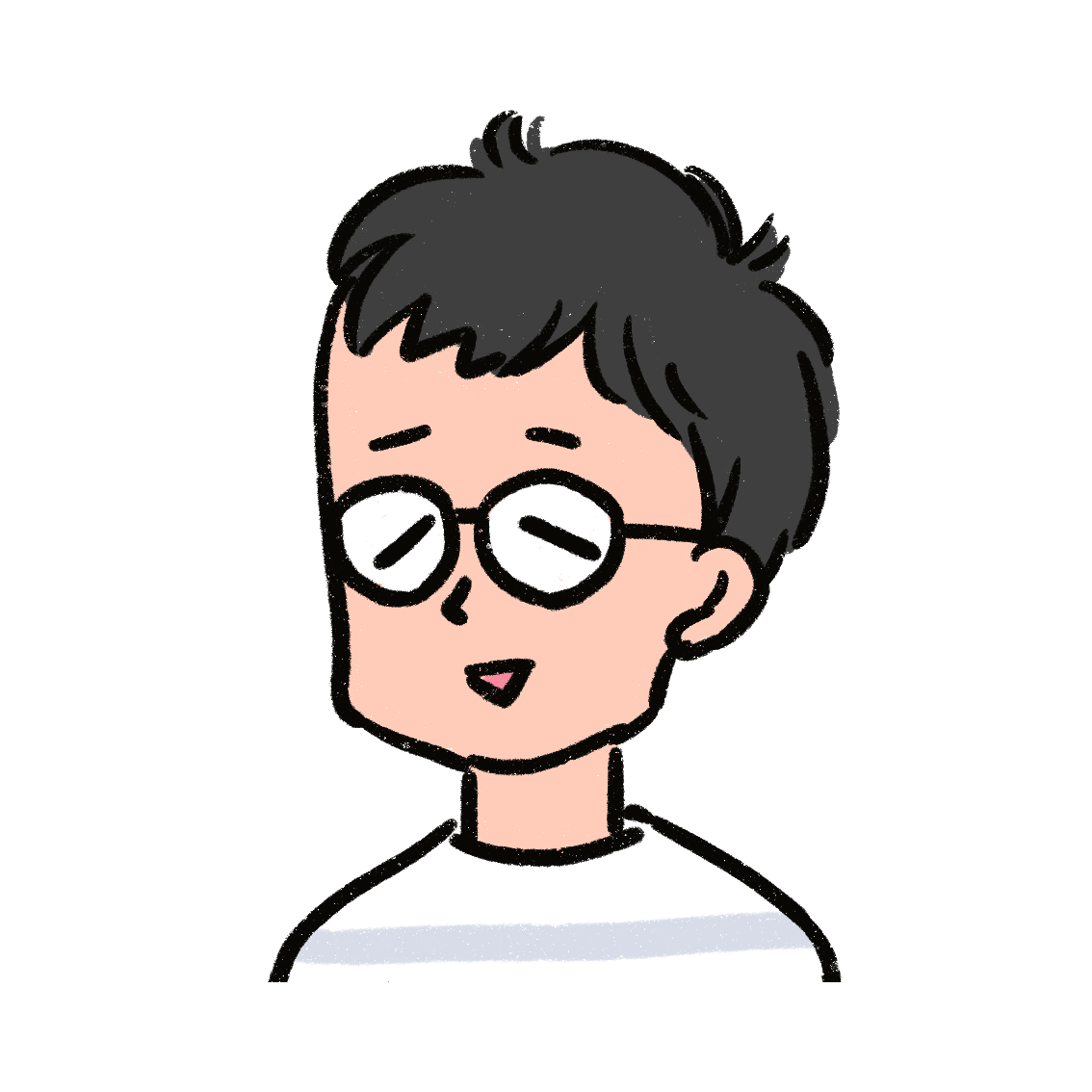
固定した地点の付近には、特異点が発生するものだと覚えておきましょう。
その上で、この特異点の応力値は無視しましょう。
集中荷重を付与した地点
解析モデルに対して集中荷重をかけると、その地点近傍に高い応力が発生します。
この場合も、実際には発生しない応力となりますので、解析結果から除外すればOKです。
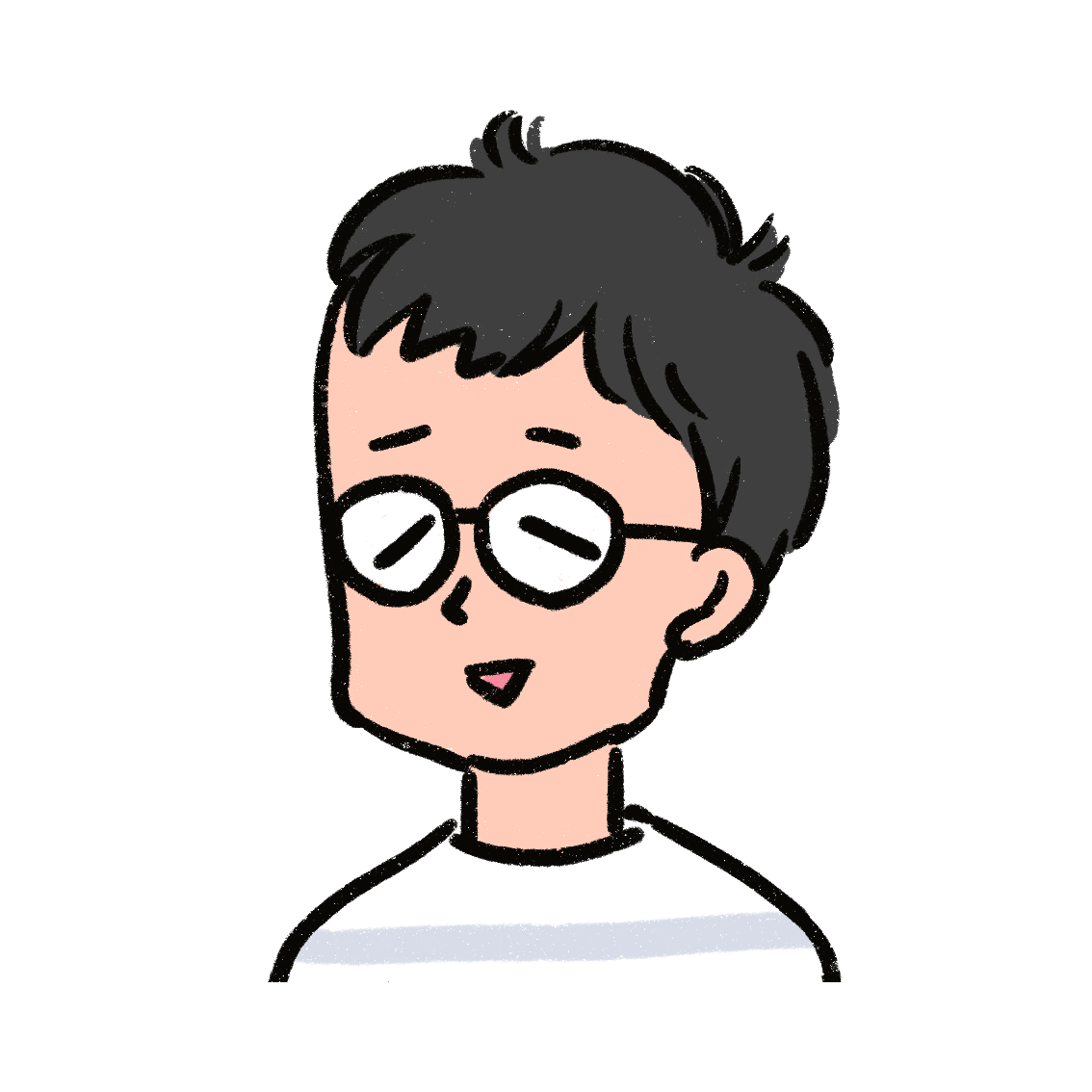
集中荷重をかけた地点の近傍も特異点が発生します。
この応力値も無視して大丈夫です。
機能性の評価
解析結果の妥当性を確認できたら、次は解析結果から得られた値(応力や変位など)が機能を満たすかどうかを評価します。
これは、許容応力や許容変位量など、比較できる基準があるため、それほど難しくはないでしょう。
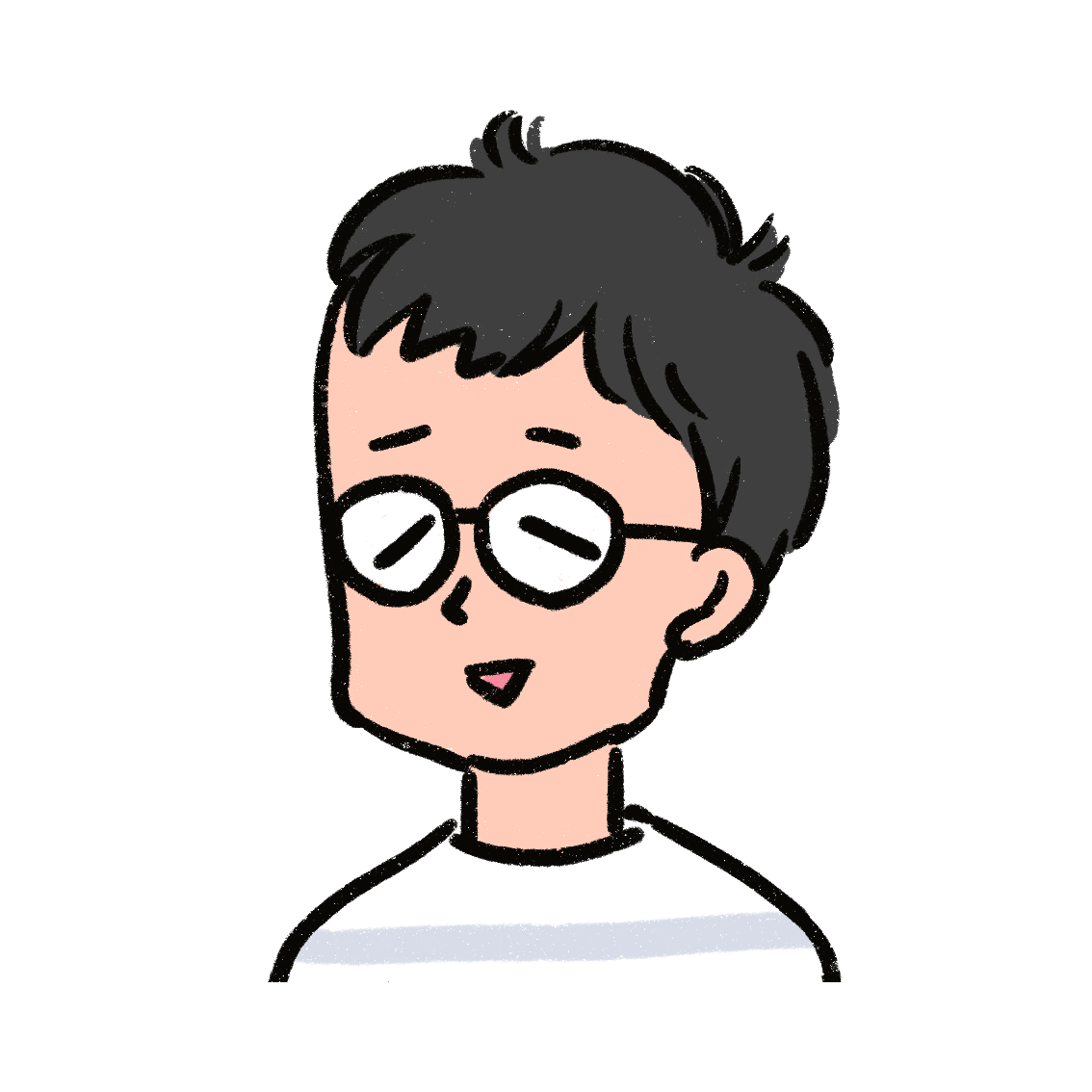
許容応力は、使用する材料の強度と安全率の決め方によって決まります。
許容変位量は、部品の機構・形状的なところから求められます。
実設計への反映
解析結果を踏まえて、実設計の形状をどのようにするか検討します。
例えば、応力の高い箇所には、補強追加や形状変更により強度UPを図ります。
逆に、応力的に余裕がある場合は、重量削減のために材料の板厚を薄くしたり、補強の数を減らしたりもできるでしょう。
応力集中が見られる場合は、切欠き形状の見直しや隅Rを大きくするなどにより、応力集中を緩和するような施策が必要です。
構造解析の結果を実設計にフィードバックすることで、より良いものづくりができます。
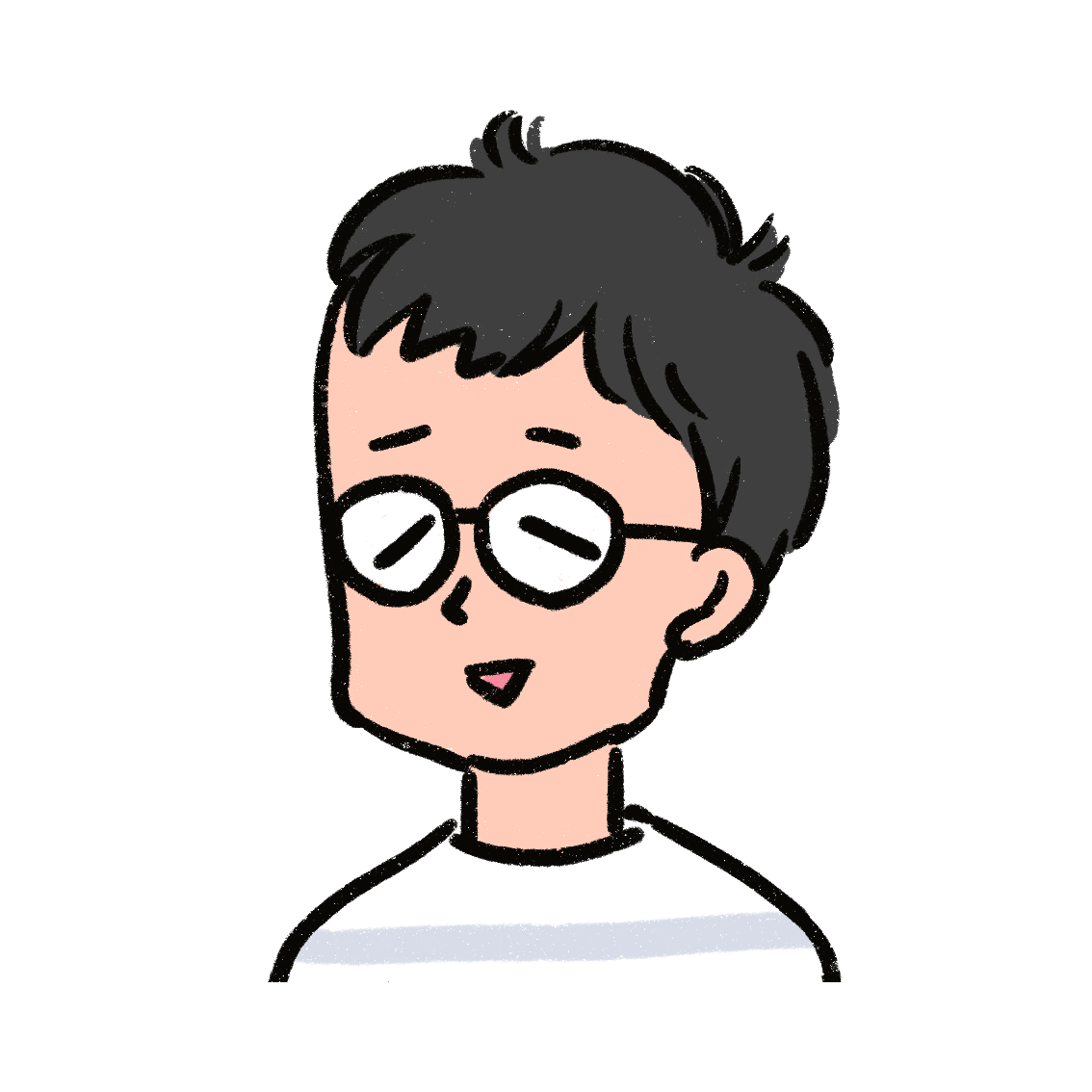
実設計に反映できてこそ、解析に価値が生まれます。
まとめ
本記事では、構造解析における結果考察の方法、とりわけ解析結果の妥当性評価について解説しました。
解析結果が妥当なものかどうかを確認する作業が、解析業務では一番重要ですし、一番大変な作業です。
ある程度の設計経験や材料力学の知識が必要となりますので、誰でも簡単にできるわけではありません。
しかし、だからこそ解析の評価ができるようになれば、設計者としての幅が広がり、職場でも重宝されるようになります。
設計者の方は、ぜひ構造解析にもチャレンジしてみてください。
最後までお読みいただきまして、ありがとうございました。
①解析の心構え、①条件設定、②メッシュ、③結果考察 の4部に分けて解説いたします。
本記事では 第4部 結果考察編 をお送りします。